Anwendung von Laser-Wegmesssensoren zur Messung des Durchmessers von Silizium-Ingots
- Teilen
- Herausgeber
- Zoe
- Ausgabezeit
- 2024/11/19
Zusammenfassung
Laser-Wegsensoren sind unverzichtbare Werkzeuge zur Messung des Durchmessers von Silizium-Ingots und bieten hohe Präzision, Echtzeitfunktionen und die Vorteile einer berührungslosen Messung. Durch Optimierung des Sensorlayouts, der Datenverarbeitung und der Umgebungsbedingungen können diese Sensoren die Messeffizienz und Produktqualität deutlich verbessern und bieten eine starke Unterstützung für die nachfolgende Verarbeitung von Silizium-Ingots.
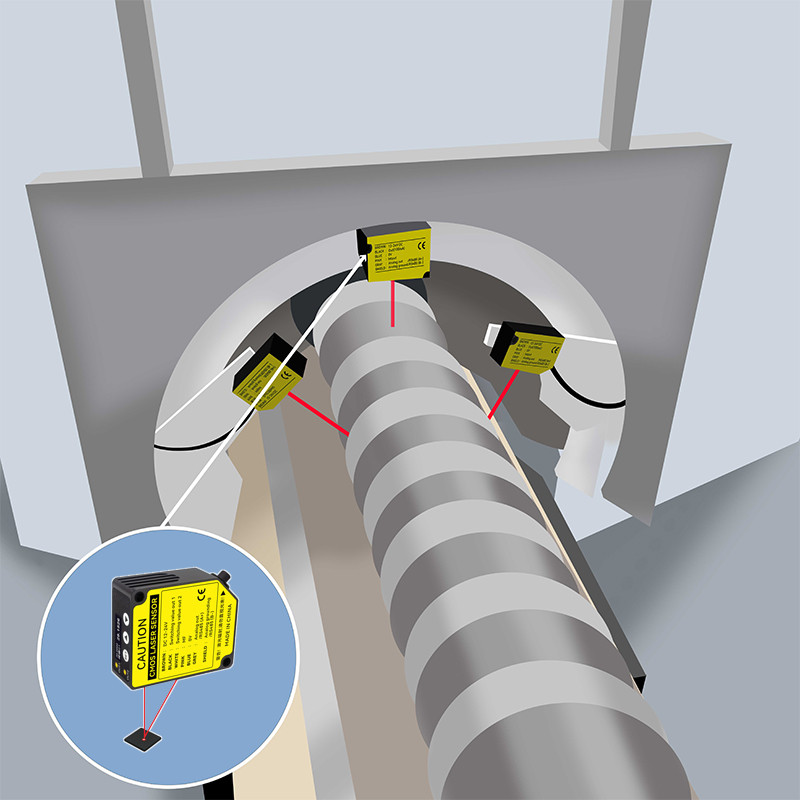
Bedeutung der Durchmessermessung von Silizium-Ingots
Der Durchmesser von Silizium-Ingots ist ein entscheidender Qualitätsparameter in der Halbleiter- und Photovoltaikindustrie und hat Auswirkungen auf verschiedene Produktions- und Verarbeitungsschritte:
Qualitätskontrolle
Stellt sicher, dass der Durchmesser des Silizium-Ingots den Konstruktionsspezifikationen entspricht, und verhindert Verarbeitungsschwierigkeiten oder Leistungseinbußen aufgrund ungleichmäßiger Durchmesser. Abweichungen über ±0,02 mm können beispielsweise die Präzision des Waferschneidens erheblich beeinträchtigen.
Waferschneiden
Bietet genaue Maßreferenzen für das Waferschneiden und gewährleistet so die Konsistenz der Dicke und Größe der geschnittenen Wafer, wodurch die Produkteinheitlichkeit und der Ertrag verbessert werden.
Gerätekompatibilität
Garantiert, dass der Durchmesser des Silizium-Ingots den Anforderungen der nachfolgenden Verarbeitungsgeräte entspricht. Dies reduziert die Rüstzeit der Geräte und verbessert die Produktionseffizienz.
Leistungsoptimierung
Der Durchmesser des Siliziumblocks beeinflusst direkt wichtige Eigenschaften wie mechanische Festigkeit und Wärmeleitfähigkeit und hat somit erhebliche Auswirkungen auf die Qualität des Endprodukts.
Gängige Methoden zur Messung des Durchmessers von Silizium-Ingots
Laser-Wegmesssensoren
Prinzip: Durch berührungslose Messung wird der Durchmesser durch Erfassung der Positionsänderungen des von der Barrenoberfläche reflektierten Laserstrahls berechnet.
Merkmale: Hohe Präzision (bis zu ±2 μm), schnelle Messung, geeignet für Online-Messungen mit Echtzeit-Überwachungsfunktionen.
Anwendungen: Ideal für Szenarien mit Hochgeschwindigkeitsrotation oder hochpräziser Online-Erkennung.
Optische Messsysteme
Prinzip: Messen des Durchmessers des Silizium-Ingots mithilfe von Bildverarbeitungstechnologie, beispielsweise durch Aufnehmen von Oberflächenbildern mit einer CCD-Kamera, und Berechnen der Abmessungen.
Merkmale: Geeignet für die Offline-Inspektion, mit höherer Genauigkeit, aber empfindlich gegenüber Oberflächenreinheit und stabilen Lichtverhältnissen.
Anwendungen: Wird in Szenarien verwendet, in denen eine extrem hohe Messgenauigkeit oder die gleichzeitige Aufzeichnung von Oberflächenmerkmalen erforderlich ist.
Mechanische Messschieber
Prinzip: Direkte Messung des Durchmessers des Silizium-Ingots durch Kontakt.
Merkmale: Einfach und tragbar, aber mit relativ geringer Präzision (ca. ±0,1 mm). Basiert auf manueller Bedienung und ist für industrielle Anwendungen, die eine hohe Genauigkeit erfordern, ungeeignet.
Anwendungen: Schnelle Feldmessungen oder Vorabprüfungen mit geringer Genauigkeit.
Anwendung von Laser-Wegmesssensoren zur Messung des Durchmessers von Silizium-Ingots
Aufgrund ihrer hohen Präzision und berührungslosen Messfunktionen sind Laser-Wegsensoren zu einer Kerntechnologie für die Messung des Durchmessers von Silizium-Ingots geworden. Nachfolgend sind die typischen Lösungen aufgeführt:
Sensor-Layout-Design
Umlaufende Mehrpunktmessung: Mehrere Laser-Wegsensoren werden rund um den Silizium-Ingot angeordnet, um gleichzeitig an mehreren Punkten Durchmesserdaten zu erfassen, wodurch die Berechnung des durchschnittlichen Durchmessers und der Rundheit ermöglicht wird.
Online-Echtzeiterkennung: Über der Produktionslinie werden Sensoren installiert, die ihre Hochgeschwindigkeitsmessfunktionen nutzen, um eine unterbrechungsfreie Erkennung während der Barrenrotation zu erreichen.
Datenerhebung und -verarbeitung
Intelligente Algorithmenkompensation: Mithilfe von Algorithmen werden Umgebungsstörungen (z. B. Schwankungen der Oberflächenreflexion oder des Umgebungslichts) korrigiert und so die Datengenauigkeit sichergestellt.
Echtzeitüberwachung und Alarme: Softwaresysteme überwachen Messdaten in Echtzeit. Überschreitet die Durchmesserabweichung einen voreingestellten Bereich (z. B. ±0,02 mm), werden Alarme ausgelöst oder Prozessparameter automatisch angepasst.
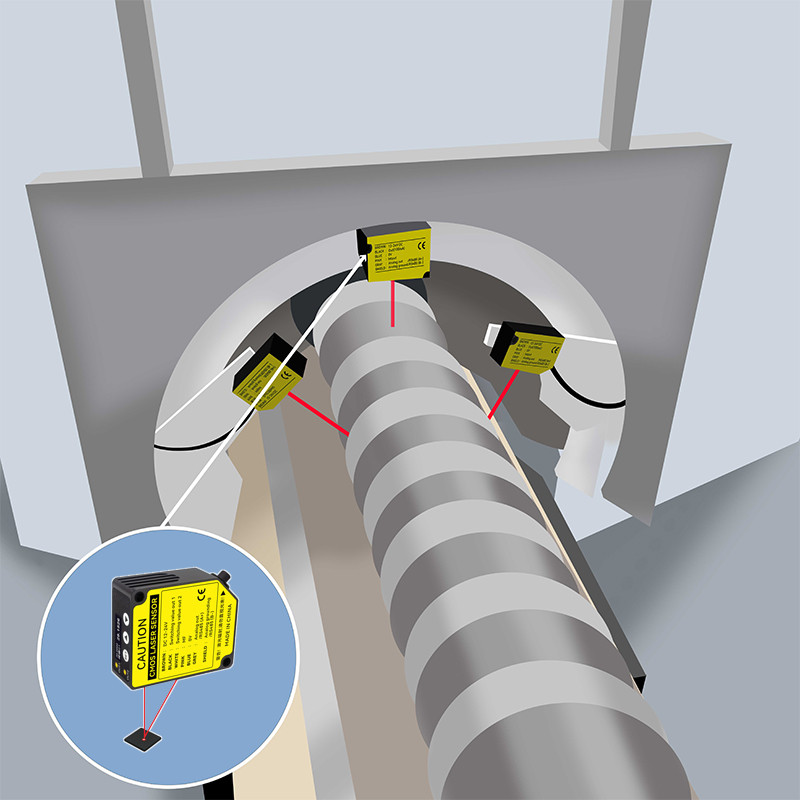
Hochpräzise Distanzmessung
GFL-G30N(P)M, (Analogausgang und Schaltausgang, Präzision: 0,002mm)
GFL-G30N(P)-485, (RS-485-Kommunikation und Schaltausgang, Präzision: 0,002 mm)
GFL-G50N(P)M, (Analogausgang und Schaltausgang, Präzision: 0,005mm)
GFL-G50N(P)-485, (RS-485-Kommunikation und Schaltausgang, Präzision: 0,005 mm)
GFL-G85N(P)M, (Analogausgang und Schaltausgang, Präzision: 0,01mm)
GFL-G85N(P)-485, (RS-485-Kommunikation und Schaltausgang, Präzision: 0,01 mm)
GFL-G120N(P)M, (Analogausgang und Schaltausgang, Präzision: 0,03mm)
GFL-G120N(P)-485, (RS-485-Kommunikation und Schaltausgang, Präzision: 0,03 mm)
GFL-G250N(P)M, (Analogausgang und Schaltausgang, Präzision: 0,075mm)
GFL-G250N(P)-485, (RS-485-Kommunikation und Schaltausgang, Präzision: 0,075 mm)